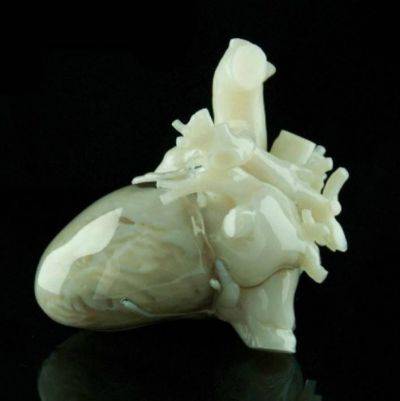
As news of the latest advancement in experimental 3D printing of tissue and organ regeneration gains attention, it would be easy to believe that 3D printing in the medical field only happens in the lab. However, new equipment and devices are being 3D printed now and in real world settings.
After years of feasibility studies, 3D printing for medical equipment and prostheses is becoming reality.
Reports have continually shown that 3D printed devices are both practical and less expensive than traditional options. For example, a University of South Florida study[i] related to prosthesis molds found that “Owing to the similarity of the 3D printed materials and the traditional materials, the 3D printed molds are easily integrated into current processing procedures.” And a UK study[ii] observed that 3D printed sensors added onto a prosthesis could help medical professionals increase comfort levels for the prosthesis wearer. In addition to better comfort, these sensors improved overall patient care.
Alan Louie, research director for IDC’s Health Insights Life Sciences Practice, which helps investors with business decisions, has this to say about 3D printing technology: “There is a lot of investment in 3D printing at the moment because there are some very clear ways that the technology can be used to improve existing processes.”[iii]
Louie sees 3D printers as a way to revolutionize medicine. “There are areas where you can determine that using a 3D-printed replacement for the current methodology can actually save money, improve healing, reduce pain, and improve overall patient care—all positive driving factors that are helping the industry move forward.”
3D Printing Improves More Than Just the Device
An example of how 3D printing medical tools reduces costs is with this bone drill that required an update to better suit the needs of both the patient and surgeon. The existing drill needed a redesign that would consistently keep its temperature low in order to avoid having to pause the procedure to let the tool cool down. The only solution available prior to the 3D printed upgrade was to pause drilling. However, with the assistance of 3D printing technology, a new drill was made using a biocompatible material “designed with their own integrated cooling ducts”. This new drill could be used for longer periods of time during a surgery. “The tests of the 3D printed bone drill determined that its use had reduced the temperature produced by drilling up to 70%”. This upgraded device has shortened the time required for surgery, saving both time and money.
The design process for medical devices and tools begins with patients, doctors, nurses, and other medical staff. They are at the forefront of the industry and keenly aware of the challenges, limitations and frustrations with existing devices. From their daily observations, efficient product re-designs and new medical device designs can, and will, transform the entire medical support field. These innovative ideas create an opportunity to improve care and support, while reducing costs.
3D printing is quickly reshaping the medical device landscape and creating more efficient tools for the medical community. Rapid prototyping brings to life product ideas that support patient care while keeping innovation at the forefront of design.
References:
[i] Jairo Chimento, M. Jason Highsmith, Nathan Crane, (2011) “3D printed tooling for thermoforming of medical devices”, Rapid Prototyping Journal, Vol. 17 Issue: 5, pp.387-392
[ii] Development and validation of a 3D-printed interfacial stress sensor for prosthetic applications. Laszczak, P. et al. Medical Engineering and Physics, Volume 37, Issue 1, 132 – 137.
[iii] https://healthtechmagazine.net/article/2017/08/healthcare-cusp-3d-medical-printing-revolution (both quotes)
About the Guest Author:
Becky Wilson writes about the applications of additive manufacturing and 3D printing, highlighting the heart in the tech. Known as Writing by Becky, she lives in Nova Scotia with her family, including two cat overlords, along with various tech gadgets – maybe adding a 3D food printer someday. You can connect with Becky on Twitter (@WritingByBecky).